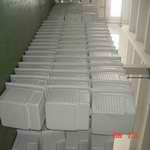
Thermofoam is a medium density white foam that is specifically non-allergenic. Its configuration is a closed cell, cross linked polyethylene and is a member of the olefin family of plastics. This configuration allows the foam to provide outstanding force dispersion equally in all directions. It is available in two densities to increase the ability of the practitioner in precise pressure application. The compression of the foam and its hypoallergenic composition lead to high patient compliance.
Manufacturing
Thermofoam has excellent, thermoforming and thermobonding characteristics. It can be knifed, die cut, or punched. It can be shaped by drape, vacuum, and pressure molding techniques. The normal forming temperature is 310 F. Thermofoam has a short heat cycle and a very short working time (.5-2 minutes). Once molded, it can be modified using localized heat.
Thermobonding is possible with all polypropylenes and polyethylenes, as well as other thermobonding materials. It may be necessary to apply a vacuum interface when vacuum forming Thermofoam, due to its good mold replication accuracy and ability to mark off. This material is self adhering at forming temperatures.
Thermofoam may not be solvent welded. Most good plastic glues will mechanically bond the foam to plastics and provide medium strength bonds to metals. Spot heat welding is possible, but not recommended for strength requiring bonds. It can be cleaned using acetone.